McKinney Concrete is a composite material made by mixing cement with aggregates and water in precise proportions. The chemical reaction is called hydration, and it makes the dry ingredients turn into rock-like hardness over nearly a month.
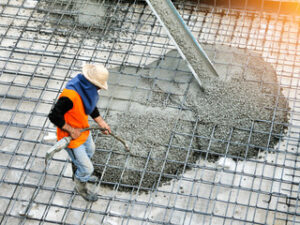
Some of the most important steps in creating a successful concrete job are choosing the right mix, placing it properly, and curing correctly. All of these factors can help to avoid problems like weak foundations or long-term durability issues.
Concrete strength is a key factor for engineers when constructing new concrete structures. It is also essential for assessing the condition of existing concrete structures to determine whether they can be safely repaired or replaced. This is because a higher strength concrete can help to increase the longevity of a structure and lower its maintenance demands.
Several factors contribute to the strength of a concrete mixture, including the type of aggregate used, the water-cement ratio, and curing conditions. Using these factors, engineers can determine the ideal concrete mix for a particular project. Depending on the desired application, specific concrete strengths pounds per square inch (PSI) are typically required by codes and safety regulations.
The most important measurement of the strength of concrete is its compressive strength. This is achieved by subjecting cylindrical samples of the concrete to various compression stages. Normally, this test is performed at seven and 28 days. The seven-day test shows early strength gains, while the 28-day test is used to calculate the final cured design strength of the concrete.
Another measure of the strength of concrete is its tensile strength. This is the ability of the concrete to resist tearing or breaking under tension. A higher tensile strength can help prevent cracks in concrete structures that undergo tensile stress, such as bridges and dams.
Concrete is a common construction material that can be found in buildings and highways around the world. It is a durable material that can withstand many types of weather, especially cold temperatures. It also resists damage from impact and vibration. In addition, concrete is easy to repair and replace if necessary.
UHPC outperforms traditional concrete in strength, making it a smart choice for new construction and repairing legacy structures. Unlike conventional concrete, UHPC is lighter in weight, which reduces the footing and support requirements for your structure. It is also easier to transport and work with than traditional concrete, which helps to save time on site and reduce labor costs. Additionally, UHPC requires fewer aggregates and portland cement than traditional concrete, so you can reduce your overall construction cost.
Durability
Concrete is a versatile construction material that’s used in everything from interstate highways to skyscrapers. It can be seen almost everywhere in the world, and it’s no wonder: this durable material has long been a staple of urban infrastructure and is capable of standing up to harsh environmental conditions. In fact, concrete structures have been known to stand for over 200 years. This incredible durability is the result of careful engineering, quality materials, and regular upkeep.
Concrete’s durability is determined by a variety of factors, including its permeability and resistance to environmental elements. A structure’s permeability determines how much water and other ions can ingress through the concrete, which in turn affects its tensile strength. A higher tensile strength means that the concrete can hold up better to abrasion and other forces.
Another factor is the resistance of concrete to chemicals. In industrial environments, concrete structures are exposed to a wide range of chemical compounds that can trigger reactions within the concrete matrix and compromise its strength. Crafting concrete mixes with a robust defense against these chemicals is crucial for maintaining concrete durability and extending its life span.
Finally, concrete must be able to withstand freezing and thawing cycles. Concrete that cracks in response to freezing temperatures can experience a vicious cycle that deteriorates the structure over time. This can lead to the formation of voids, which encourage moisture and CO2, which incite corrosion of steel bars embedded in the concrete.
To address these issues, engineers have developed new types of concrete that can withstand abrasion and other forces without compromising its durability. In addition to traditional concrete, new technologies like fiber reinforcement and advanced admixtures allow architects and engineers to create more resilient structures that can withstand the tests of time.
Durability is important because it protects people from natural disasters, such as earthquakes and hurricanes. It also allows architects and engineers to design buildings that are more energy efficient, saving both money and resources. This is especially true when buildings are built using sustainable concrete. Sustainable concrete is made with recycled materials, and it can last for up to 100 years.
Flexibility
Concrete is the most widely used building material on the planet, but it can be brittle and heavy. To overcome these challenges, engineers have been developing a flexible concrete that can bend without cracking. The technology is based on the natural elastic polymer that lines the inside of abalone shells. It’s hoped that this new type of concrete will improve safety and help save lives in earthquakes.
A flexible concrete mix contains silica, asbestos, glass, and steel fibers that provide elasticity. It also uses Portland cement that is similar to the kind used in traditional concrete. The mixture is prepared by adding water and mixing. The concrete is then poured onto a form. The concrete is allowed to dry before it’s removed from the form. It can be used for a variety of applications. It can be molded into different shapes and can be used for sidewalks, driveways, and flooring.
The main advantage of flexible concrete is its ability to withstand a wide range of temperatures. Its tensile strength is more than twice as high as conventional concrete. This makes it suitable for use in bridges, tunnels, and roadways. In addition, it is much less prone to cracking than conventional concrete.
Another benefit of flexible concrete is that it can be built in a shorter time frame. This allows builders to complete large sections of a project in a short time. It can also be molded into different shapes to accommodate unique designs. It can be made aesthetically appealing with the use of decorative concrete techniques, such as staining and stamping.
This type of concrete is also better for the environment than traditional concrete. It uses fewer raw materials and produces fewer harmful gasses. It also weighs less, which reduces the cost of transporting and handling it. It is available in a variety of colors and finishes to suit any style of building.
This is the latest in a series of innovative technologies for concrete. Other recent developments include concrete that can heal itself and self-heat, which could be useful in road construction.
Cost
Concrete is a popular building material that has many benefits. It is strong and durable, and it is also energy efficient. It can be used to build walls, floors, and even foundations. Concrete is also easy to clean and requires minimal maintenance. However, there are some things to keep in mind when choosing concrete for your home or business.
Concrete can be made in a factory or on site. In either case, the process must be carefully controlled to ensure that it is ready to use within a specified time period. This is especially important for large projects, like dams and airport runways. In addition, concrete must be poured within a certain temperature range to achieve the desired strength.
The cost of concrete varies depending on the type and size of the project. A good rule of thumb is to plan for 5% to 20% more than your actual construction costs, as this allows you to avoid unexpected expenses. This is especially important when working on a tight budget.
In recent years, the concrete industry has been committed to reducing its carbon footprint through a number of initiatives, including the development of low-carbon cement and improved energy efficiency in buildings. In addition, it is possible to construct concrete structures using prefabricated components, which can significantly speed up the construction process and improve quality control.
In addition to being durable, concrete is also fire resistant, making it a safe and healthy choice for building occupants. It can also help reduce airborne allergens, such as dust and pollen, which can trigger asthma symptoms. Concrete is also inert and does not rot or mildew. This makes it an environmentally friendly alternative to wood construction materials.
Concrete is an excellent insulator and can save 5% to 20% in operating energy costs, compared with softwood lumber. This is because of its high thermal mass, which helps regulate interior temperatures and save energy costs. Moreover, it can help reduce noise pollution by reflecting sound waves and providing a quiet environment for occupants. This is why it is commonly used in noise barriers along highways and in building interiors.