Plastic Injection Molding Florida is a manufacturing process that can produce multiple parts in one cycle. This makes it ideal for high-volume production. However, an upfront investment in tooling is required.
There are many types of thermoplastic resins to choose from. Fictiv has design and production experts ready to help you choose the right material for your application.
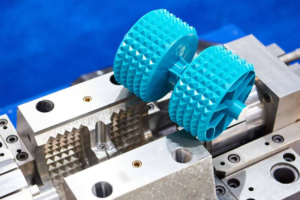
Plastic injection molding is a cost-effective manufacturing process that can produce high quantities of products quickly and efficiently. The key to minimizing costs is understanding how the process works and making smart design choices. It is also helpful to understand the factors that determine the final injection molding cost. This will help you budget properly and avoid surprise expenses.
The first factor that influences the price of a plastic injection mold is the size of the product. Larger parts require larger and more expensive molds, which can increase production costs significantly. In addition, larger parts can take longer to make and may need to be made from a harder, more durable plastic to ensure they retain their shape and durability.
Another important factor that can impact the plastic injection molding cost is the type of thermoplastic that will be used. Different plastics have varying cost-efficiency characteristics, and each has its own benefits. For example, polypropylene (PP) is a very affordable plastic that is ideal for many applications. However, the choice of a plastic should always consider the specific application in question to achieve optimal performance and cost efficiency.
Injection molding is a fast and efficient process that can be used to create complex, custom plastic components. However, the upfront cost of designing and fabricating a plastic injection mold can be prohibitive for some manufacturers. In order to reduce the costs associated with the manufacturing process, manufacturers can use 3D printing technology to fabricate prototypes that can be used as injection molds. This method is inexpensive, quick and efficient, and allows engineers to test and iterate their designs before investing in hard tooling for mass production.
Injection molding is a process in which a thermoplastic is melted to a liquid state, then injected into a customized, double-sided mold using a high-pressure injection tool. The resulting part is then cooled and ejected from the mold. This process is incredibly efficient because it can produce large volumes of parts in a very short amount of time, which is a benefit for businesses that need to turn around orders quickly and effectively. In addition, it is possible to recycle the unused plastic, which can further reduce costs.
Durable
The durability of injection molds depends on many factors, including the environment, maintenance, materials, structure, molding conditions, and design. For example, if the injection process runs too fast, it can cause undue stress to the mold. This stress can damage the plastic part and also lead to failures such as sink marks, flow lines, and surface delamination. To reduce this stress, manufacturers use slow cycle times to prolong the life of the injection mold. This not only improves production efficiency but also helps increase possible revenue and profit margins.
The first step in the injection mold making process is to create the tooling, which is a metal block that acts as a negative of the plastic part. Then engineers mill the tooling with a CNC machine, which carves out a pattern that will form the part. Once the tooling is ready, the injection process can begin.
Injection molded plastic parts have several advantages, including durability and versatility. Polycarbonate (PC), for instance, is strong and light. It is also resistant to chemicals, moisture, and bacterial growth. It is available in clear or pigmented versions and has good dimensional stability. However, it is not suitable for outdoor applications because it does not hold up well against UV radiation.
Another durable plastic is polyethylene (PE). PE has excellent impact strength, is chemical-resistant, and can withstand low temperatures. It can be used for a wide range of applications, from water bottles to automotive components. It is also easy to recycle, and it can be molded into a variety of shapes and sizes.
Other durable plastics include acrylonitrile butadiene styrene (ABS). ABS is a popular material for consumer products, such as toys and kitchen appliances. It is very hard and lightweight, yet still flexible. It is also resistant to chemicals, moisture, bacterial growth, and gamma radiation.
Versatile
Plastic injection molding is one of the most versatile production methods, capable of producing a wide range of products and parts. Its versatility is largely due to the high pressure during injection, which allows for complex and intricate designs that would otherwise be difficult or impossible to manufacture with other manufacturing processes. It also offers the flexibility to experiment with unique shapes and internal channels, pushing the boundaries of what is possible in product design.
Injection molding is a great process for prototyping, as it allows you to test your designs quickly and efficiently without having to worry about budget-busting tooling costs. It’s also a good choice for production, as it is able to produce large quantities of the same part quickly and reliably. Injection molding is available for both thermoplastics (which can be re-heated and re-molded many times) and thermosets (which form irreversible chemical bonds during the curing process).
When designing your product for injection molding, it’s important to consider the production process that will be used and any limitations or requirements of that process. For example, you’ll want to make sure your design includes features such as bosses for threaded inserts or fasteners, hollow sections where needed, ribbed supports, snap-fit joints or friction fits as joining elements, living hinges, and draft angles on vertical walls. This will help you to avoid any unnecessary assembly and improve the efficiency of your production line.
Once your design is finalized, it will be converted into a digital format for the injection molding process and then a tool will be built to create the mold that will ultimately produce your product. A well-equipped injection molding company will have an in-house tool room to ensure that your project goes smoothly from initial concept to final delivery.
During the injection molding process, pelletized raw material is fed into a heated barrel using a reciprocating screw. This process heats the polymer, reducing its viscosity and breaking the Van der Waals forces that resist the relative flow of individual chain molecules. The screw then mixes and homogenizes the thermal and viscous distributions of the polymer before delivering it to the injection nozzle through a runner system.
Environmentally Friendly
Plastics are often associated with environmental harm, but sustainable injection molding is helping to mitigate these concerns. By incorporating recycled materials and reducing energy consumption, manufacturers can reduce their impact on the environment while also reaping benefits like cost savings and regulatory compliance.
The manufacturing industry as a whole has been working hard to create more sustainable working processes in recent years. This is due in part to the growing plastic pollution problem around the world. However, plastic injection molding isn’t immune to these issues, and many companies are looking for ways to create more sustainable plastic products.
One way to do this is by using eco-friendly plastics that are made from renewable resources. These green plastics are made from biopolymers such as polylactic acid (PLA) and polyhydroxyalkanoates (PHA), which are derived from plant-based materials such as cornstarch or sugarcane. These plastics not only cut down on the reliance on fossil fuels but also decrease carbon emissions during production. In addition to this, some plastics are now being developed that can be broken down by microorganisms in the natural environment, which further cuts down on waste.
Another sustainable option is to use recycled plastics, which can be reused in the manufacturing process without losing their quality or function. In addition, facilities that utilize lean manufacturing and Design for Manufacturing principles can minimize waste by reducing the amount of excess material known as sprues that need to be discarded. Many plastic injection molding experts, including Fern Plastics, have in-house granulators that allow them to recycle these sprues into new plastic material for future projects.
Finally, utilizing renewable energy sources to power manufacturing plants can drastically reduce carbon emissions. Additionally, optimizing logistics and reducing transportation distances can further reduce emissions. These steps not only improve the company’s environmental impact, but they also demonstrate a commitment to sustainability and a desire to make a positive impact on the planet.
In the future, it will be crucial that manufacturers adopt more sustainable practices to help protect our planet. By embracing innovation, leveraging energy efficiency, and utilizing sustainable materials, companies can greatly reduce their carbon footprint while also reaping the financial benefits of reduced operating costs and enhanced brand reputation. When choosing a plastic injection molding company, you should ask them about their commitment to sustainability and look for proof of their achievements.